This post is also available in:
Danish
Lean management is a system and mindset that gives greater productivity and better motivation among employees. Lean comes from car industry, but it also produces really good results on agriculture. We have seen 10-20% improvements in work efficiency in just one year. We also look at much better communication and fewer mistakes and misunderstandings on the farm. It simply gives employees more satisfaction when they can help reduce waste in their work day.
Lean Farming® creates higher productivity in agriculture
All of the activities and consulting services Lean Farming® offers have the overall goal of creating higher productivity for you as a farmer and for you in the agro-industry.
This happens especially when we work with
- Production planning with flow optimization and work procedures
- Animal welfare, which creates better production conditions for the animals
- Motivation of employees because they get involved and take responsibility
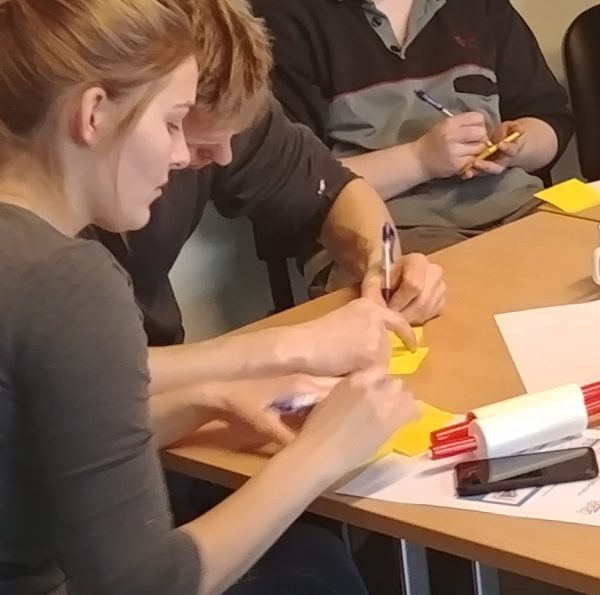
You can achieve that with Lean
Lean can provide higher productivity and lower costs. The lean thinking is that you must eliminate waste in production and processes. We do this by using some completely systematic methods and tools. But it also engages employees in a whole new way. They get involved and their contribution matters. We receive reports that employees also take more responsibility in their daily work.
If you are a little curious about what Lean can do for your business. I would like to come to an introductory meeting or I will make a presentation for you and your employees. I keep many posts for large and small assemblies.
I also often do workshops for a group of employees at a farm. The theme is always chosen by the farmer as there are no two challenges that are the same.
If the desire is a complete implementation of the Lean approach to agriculture, then we will start with a plan and agree on the process. Sometimes I’m very involved, but most often my role is to coach the coach.
Sometimes we take one visit at a time and sometimes we agree on a longer course. You can always get a fixed price on a course so you are fully aware of the cost. After the first visit to the farm, I can also do a cost-benefit calculation so you can see what you can expect to get out of the process.
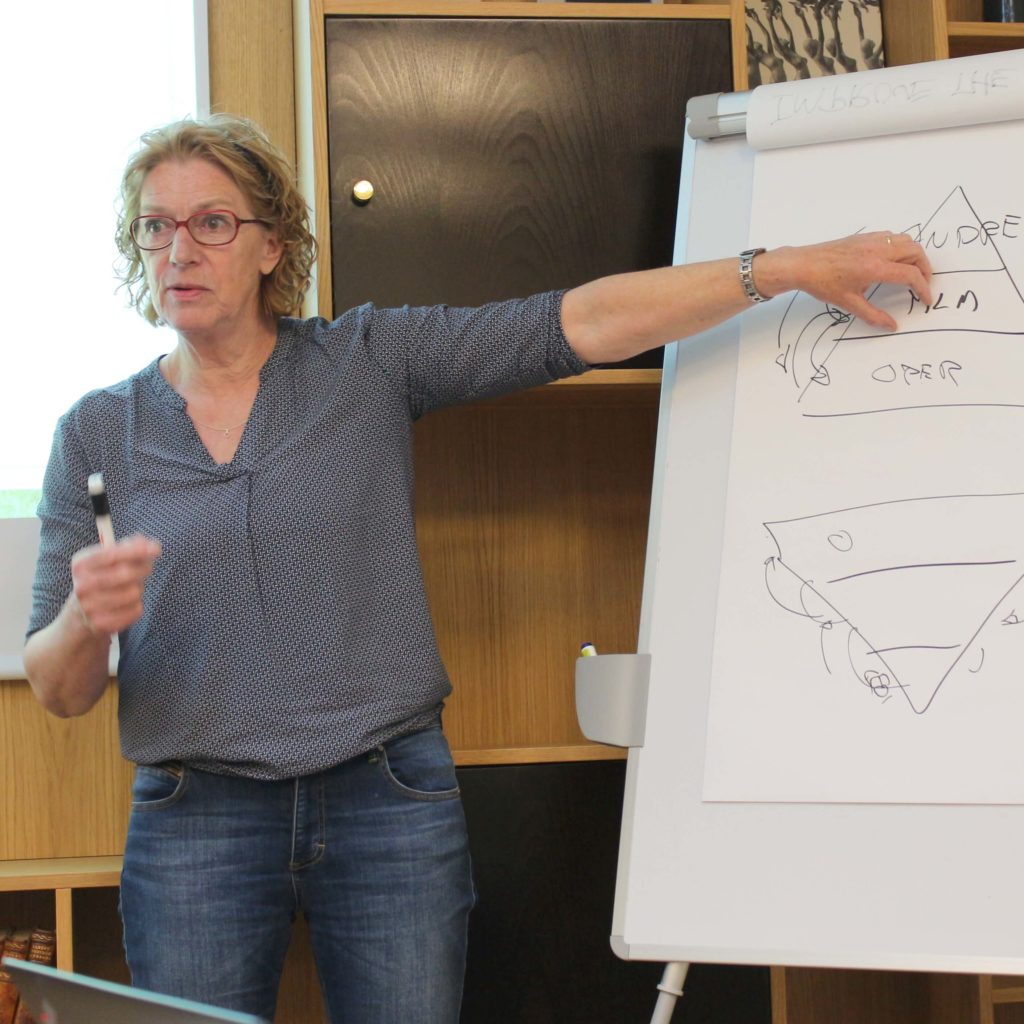
Presentations and workshops on Lean
I hold many presentations and workshops on Lean in both small and large assemblies. Many people are initially curious about what Lean is and what Lean can do for their farming.
The small assemblies may be the employees of farm or a discussion group. I have also given presentations for hundreds of people where it was organized by a company or organization.
The purpose of the lecture and workshop is for the participants to get inspiration and learning. I always use a lot of pictures and examples from practical farming. If possible, Lean games and other participant activities are also included.
A workshop on a farm with several participants can take place in such a way that after a brief presentation about Lean in general we visit the farm. We see, for example. a work process such as milking, feeding, castrating or harvesting. Participants work in groups and record time, make a spaghetti chart, record video, etc. and then chart the process of finding wastes and improvements. It activates all participants and gives a really good insight into what Lean is for.
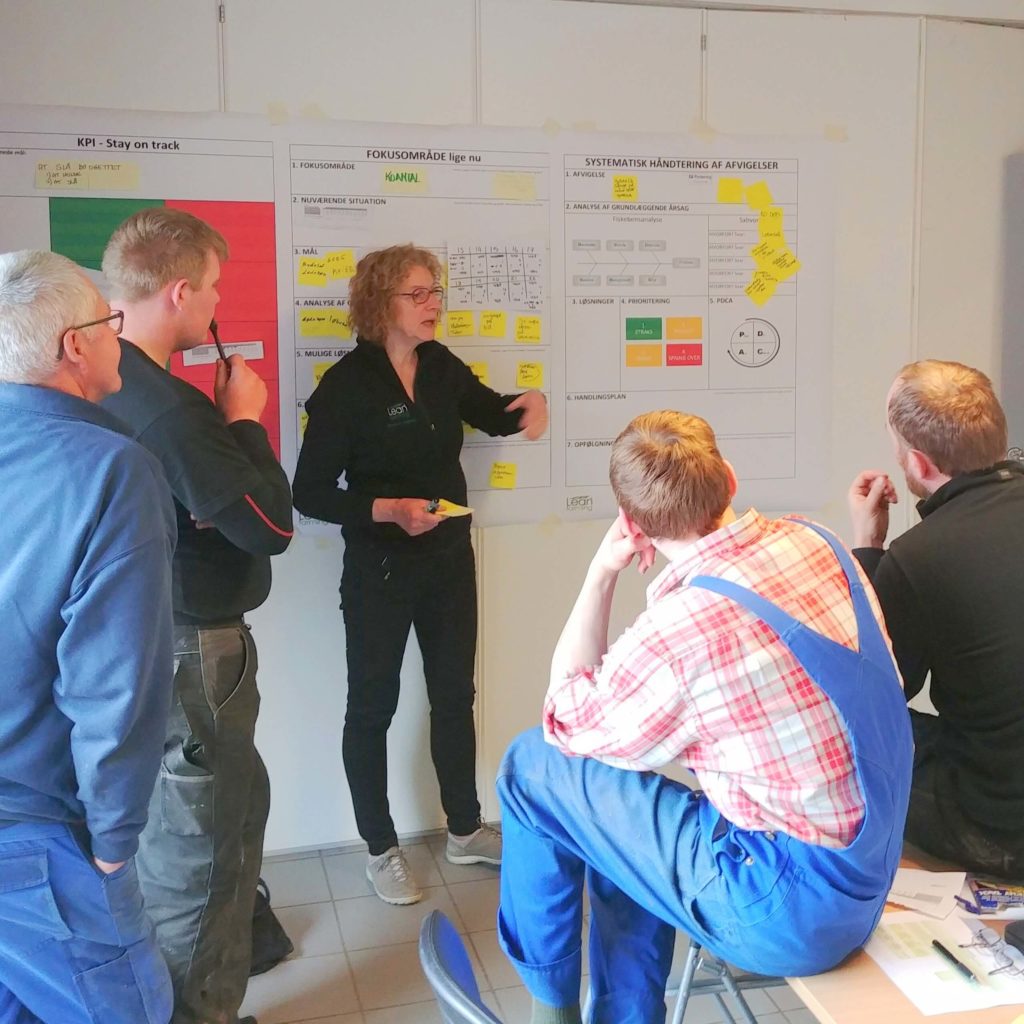
Training of employees
When employees need to get involved in the right way, it is a good idea to train them in the tools. They must both understand and practice.
Initially, it may be a 3-hour workshop to understand what Lean can do and gain an insight into the mindset.
Later we will implement various tools such as board meeting, value stream mapping or as in the image “Visible Target Management”.
If we take “visible goal management” as an example, so will wetraditional managementbe such that the manager informs the employees of the results achieved and tells what to do in the comming weeks.
With Lean management the method is different. You choose a focus area that is related to your overall goal. Employees are involved in finding waste in the process or procedures, testing solutions and making measurements of the effect daily or weekly on a board.
That method requires education and training.
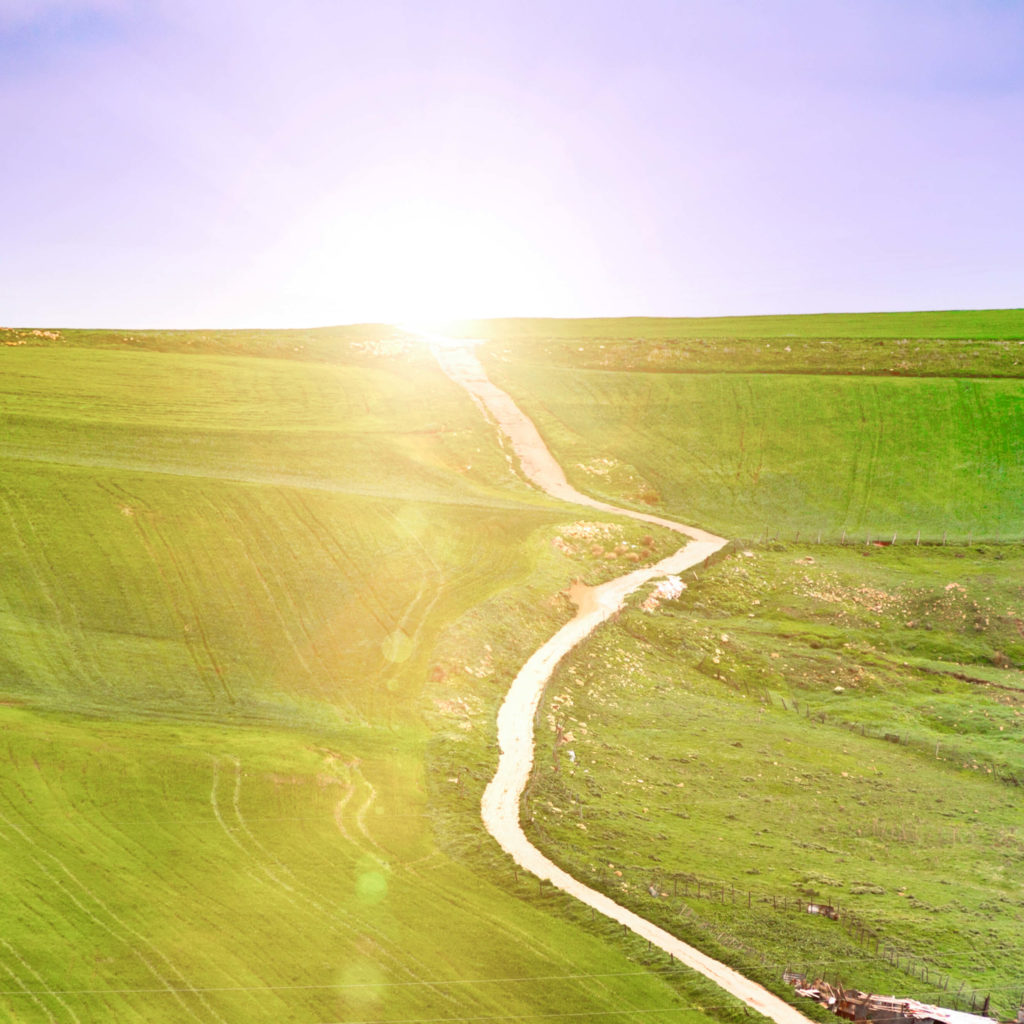
Lean implementation step by step
For those who want to implement Lean as a management system anywhere in your business and where the culture is Lean, an implementation can be done in the following steps:
- We start with a review of your agriculture and a discussion of your Lean Vision , what you want to achieve with Lean.
- Together with your middle managers, we have a Kick-off meeting where they learn about the Lean mindset and we set a plan for implementation.
- You and the middle managers set goals for the company as a whole and for the individual operations. I would recommend that we start with the area that you think is most important to get improvements on e.g. productivity, quality, cost or maybe safety. It can also be communication and employee satisfaction.
- We train you in the tools you need. First it is the operators and then they train their team. We often start with a team as a pilot project for 2-3 months.
- Then we roll out the project in the other areas of your business.
- We measure the outcome, adjust and implement the new procedures.
- We stabilize the positive outcome by teaching middle managers how to train the new standards and how to continue to improve.
- You are now ready to take up new focus areas so you can continue to improve your business. If you have started with productivity, it may be safety next time – or vice versa.
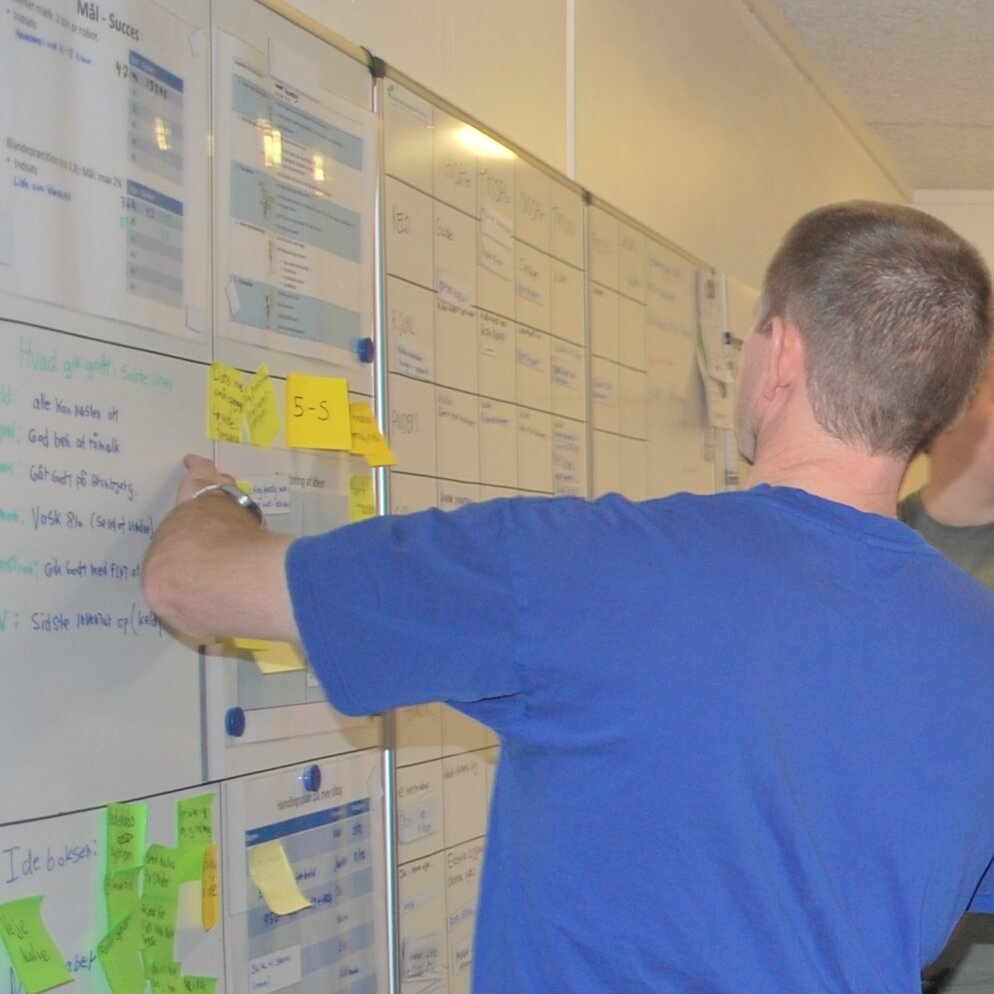
Lean in small bites
A complete Lean implementation can be a big handful. But it can also be possible to take it in smaller snatches. You can start somewhere and possibly let it spread from there.
I always take the challenge that the farmer thinks is most important right now. It is important that we quickly reach some results in the area that is the “burning platform”.
I can give some examples:
- We have too much fire figthing and things that break down: Then we start by building structure into the planning of tasks and preventive maintenance on fixtures and fittings.
- I can’t get employees to follow the same procedures : Then we start by doing SOPs (Standard Operation Procedure) and train with TWI (Training Within Industry).
- We need to be much better at productivity and efficiency: Then we start with the whiteboard meeting and learn how to do value stream mapping to eliminate waste in the processes.
No matter what we start with, measurements are absolutely necessary. We measure what you want to change. We measure before we start and along the way with daily or weekly measurements. Measurements are absolutely necessary to see if it works or not. It is also more motivating.
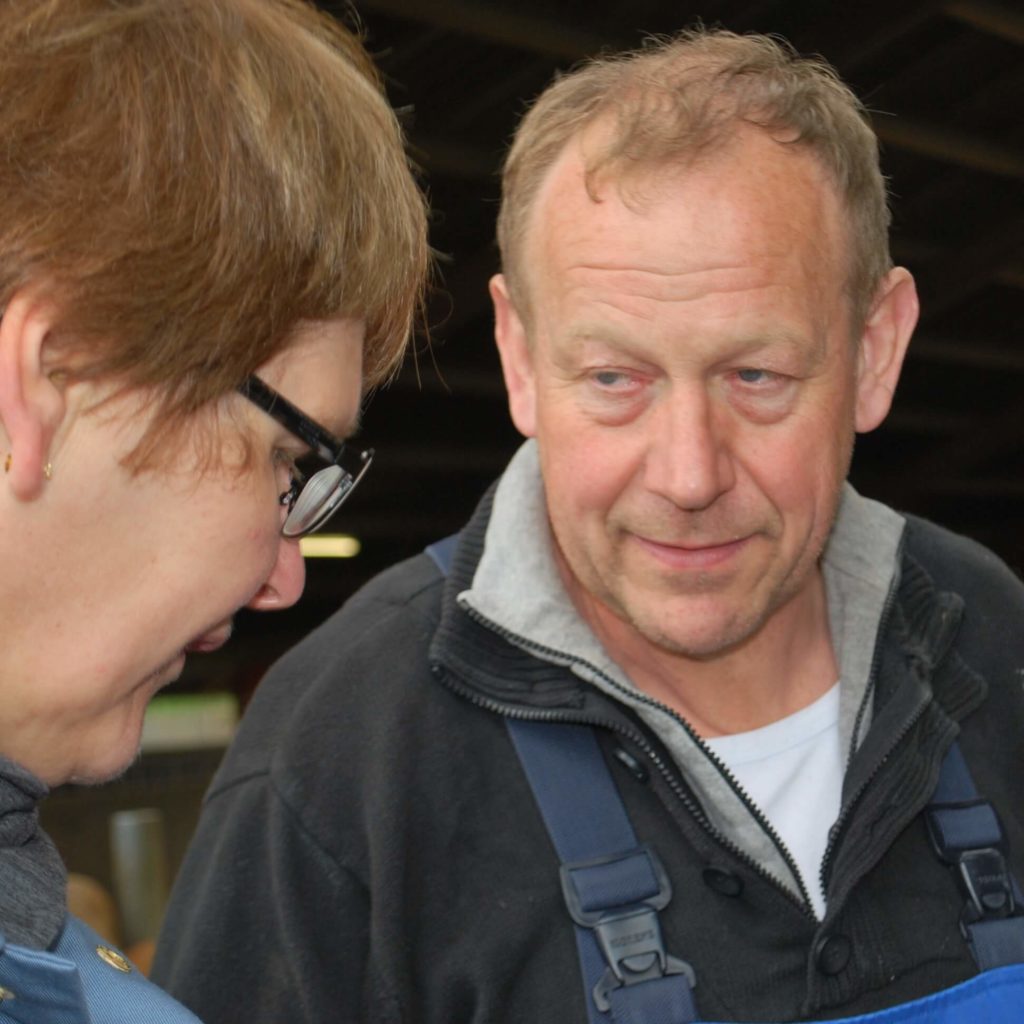
What others say
- We have saved half a man compared to last year
- Our employees take much more by themselves and I save a lot of time
- It is really a pleasure that we have been put in order. We save a lot of time because we don’t have to look for things anymore.
- We have reduced working hours by 10 percent over the past 9 months.
- It has calmed down after we had done more structure on the tasks.
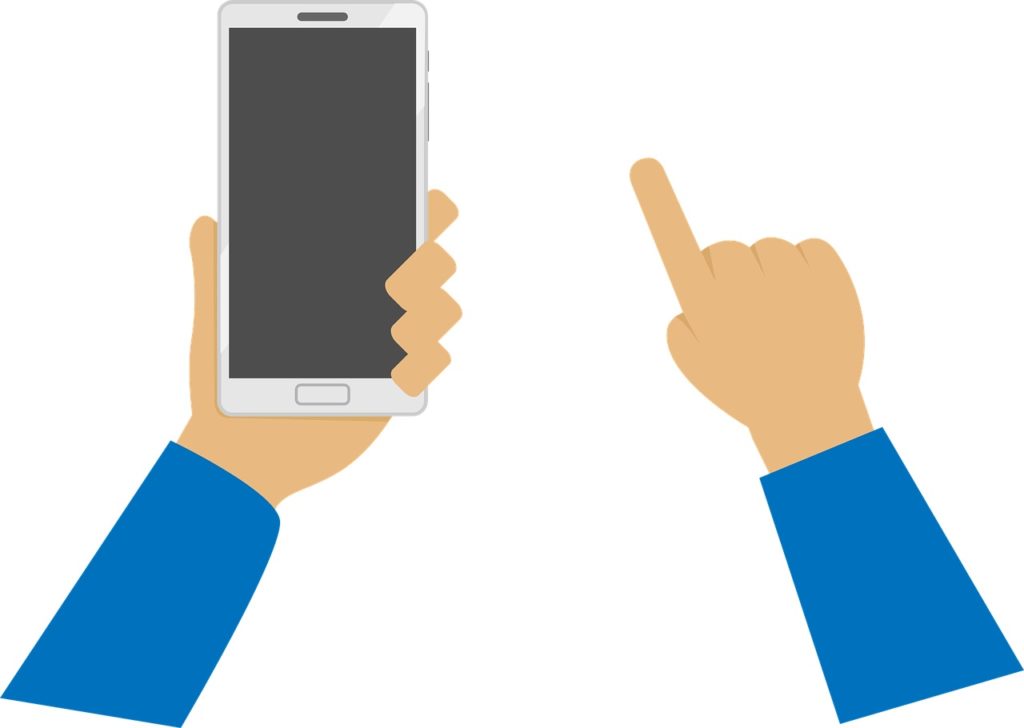
Want to know more, contact me