This post is also available in:
Danish
Do you know the expression: “Work smarter – not harder”? Yes, and then most people think, how can you do that? It is not so easy without using a system. That system is called Lean Management. It is, therefore, necessary to read and learn something about the system to use it.
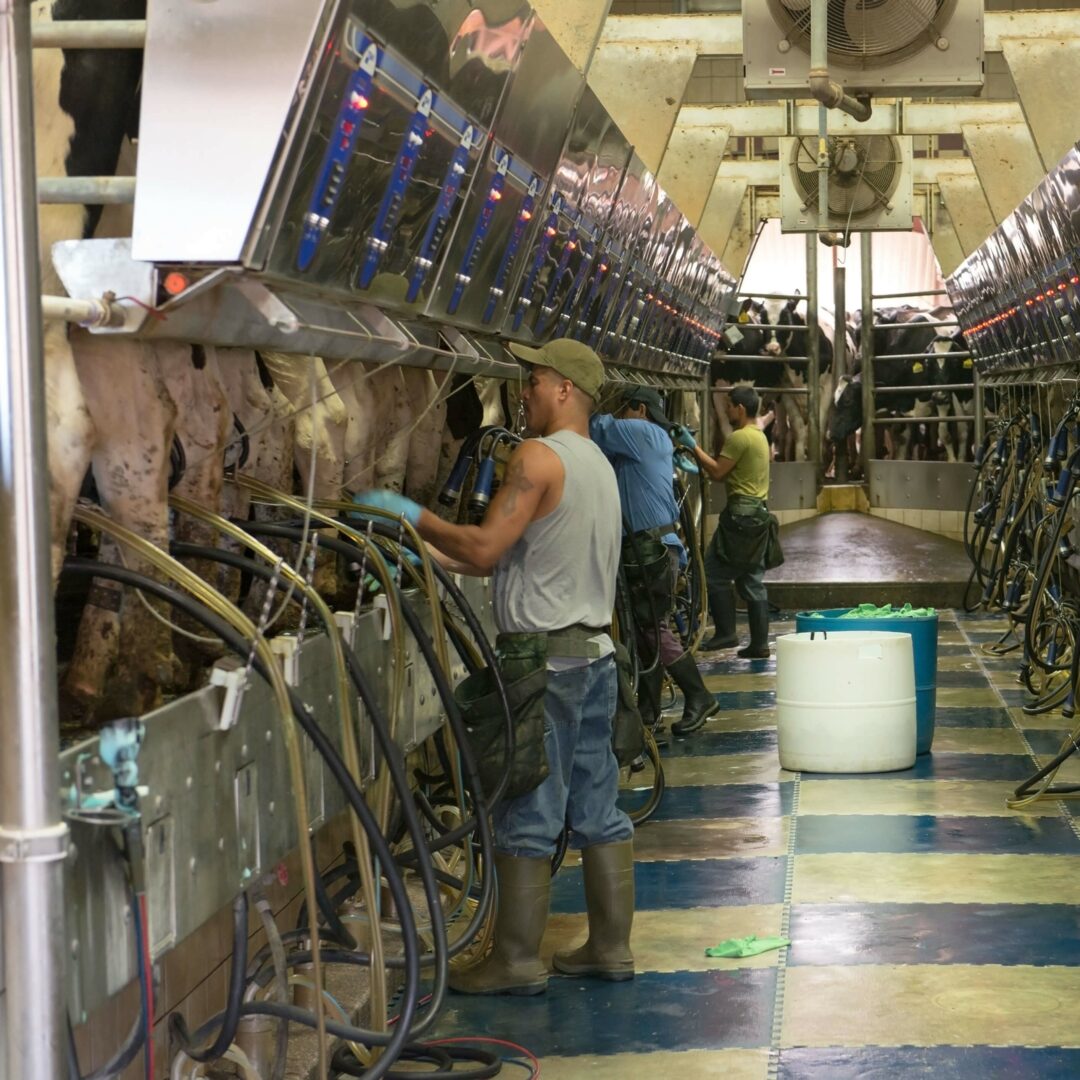
The processes must be streamlined
Lean means without anything extra. Work processes must be streamlined so that you only do what creates value. The machine park must be cut to the bone, so you only have the necessary costs. Your inventory should be as small as possible because inventory costs money.
That way, you can make your farm more efficient.
There are eight types of waste.
We call the activities that do not create value waste. To become more efficient, learning what waste can be is necessary. Therefore, wastes are divided into types, making learning more accessible.
Why is it difficult? It is because we get used to doing things a certain way. Then, we cannot always imagine that it can be otherwise.
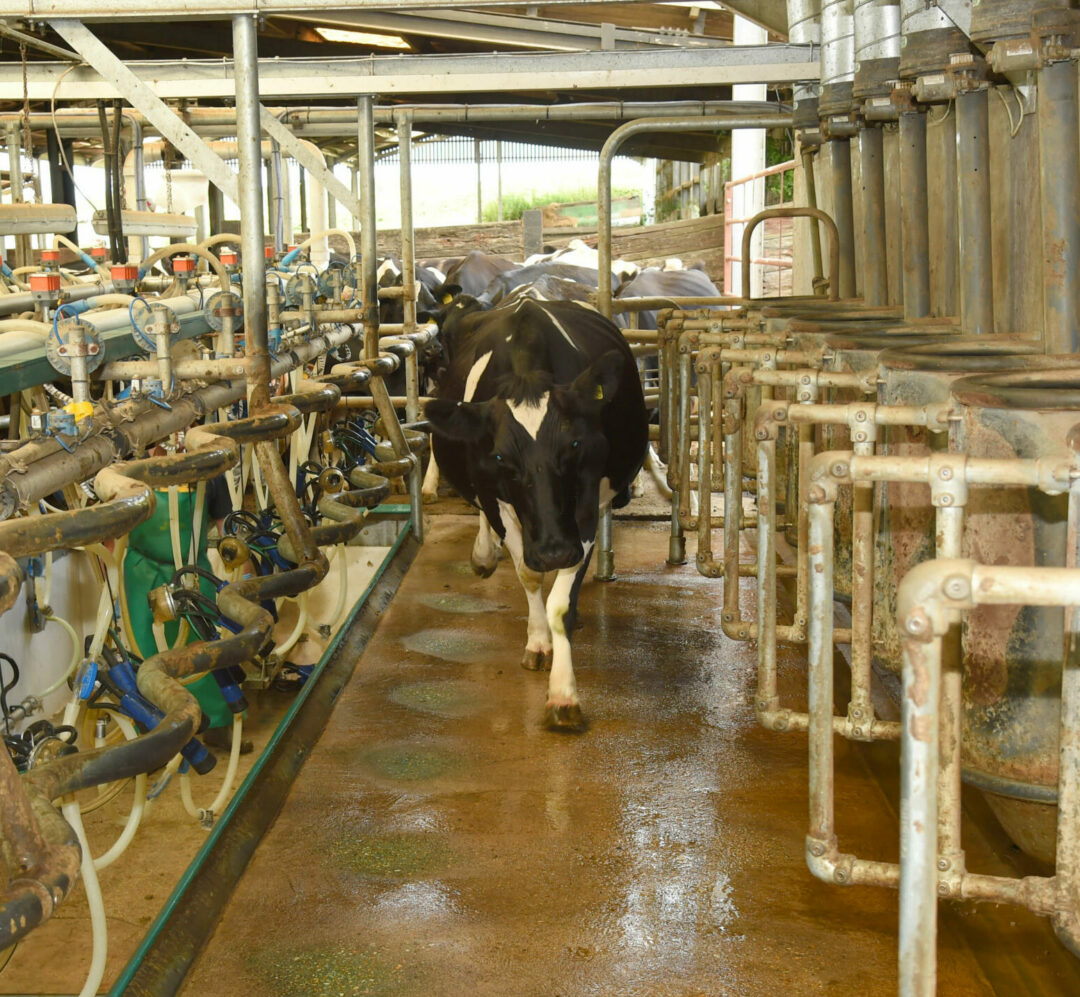
1. Defect
Defects are the first type of waste. Here, we are talking about defects in production. Sick animals and dead animals fall under this category. It is also a defect when the feed gets hot, or there is mould in the silo. Due to poor communication, the defect can happen when a trucker unloads at the wrong place.
2. Overproduction
Overproduction is a type of waste because it does not create value. It may be that you must discard some feed because you have fed too much. Or when you must discard some powdered milk that has been mixed. It is overproduction when you have produced more feed in the field than you need. Although it can be saved for later, it is an additional cost for production, and it can be ruined.
3. Waiting
If you have some workflows where you must wait, it’s a waste of time. This can happen when a person must wait for water to run in a tank or when a cow must finish in the robot. It is a waste of time when an employee stands and waits for a machine he needs to use. In the milking parlour, we see waiting times when the number of people is not always adapted to the workflow.
4. Non-utilized talent
It is a waste if you do not ask your employees for their opinions and ideas for improvement. They certainly have suggestions for doing the job better because they do it daily. But if that knowledge never emerges, it is a waste. It can also be a waste if someone is misplaced and does not use their abilities properly.
5. Transport
On a farm, transport takes place all the time. It is an art to adjust it so there is no waste. Transport is creating waste if too many transports and too large or too small wagons. Logistics is essential, and it is straightforward with the location of the feed. If there are many feed items to be mixed and they are not in the proper location to each other, it can cause waste. The same applies to the transport of animals when the young stock is moved too many times.
6. Inventory
Storage costs money in both liquidity and space. Therefore, inventory must be kept as low as possible to reduce costs. It might be nice to have a good stock of, for example, spare parts, but it costs money, and you might not be able to find it anyway when you need it. A large inventory often occurs when you buy a lot for a cheaper price. But there is a risk that something will have to be discarded again before it is used.
7. Motion
If there are unnecessary movements in a workflow, it is a waste. It can occur when things are not positioned correctly in relation to the task. If an employee must go down to the other end of the barn to find the scraper. It is also a waste if an employee must go around looking for things that are not in their place.
8. Extra-processing
As a farmer, you will probably think you never do more than necessary because there is no time for that. But ploughing is an example of a work process that is carried out even though it is not always needed. In the office, many people still print papers and put them in ring binders, even if it is stored online. It is also an example of extra-processing.
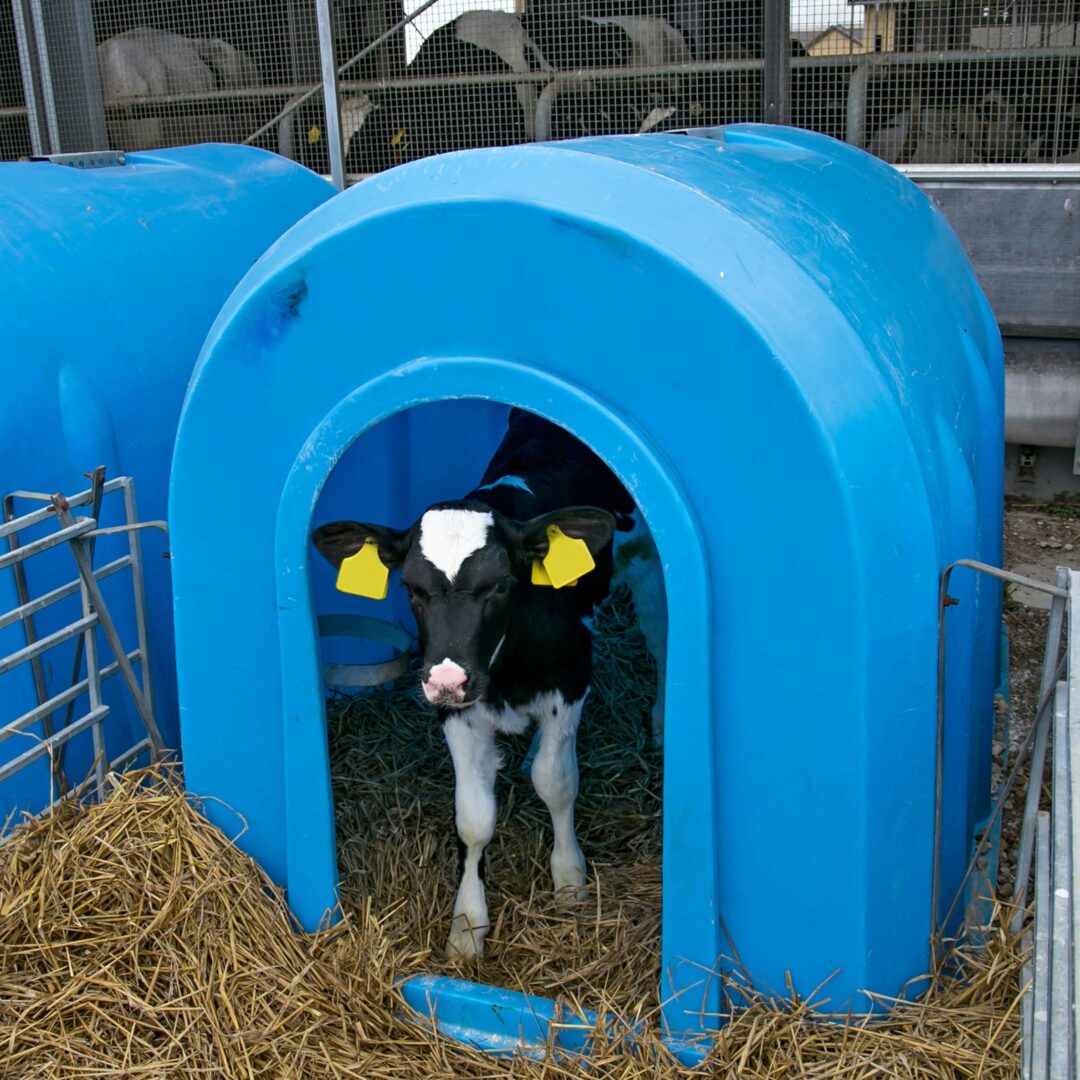
Many small steps lead to improvements.
You can’t eliminate all waste with the snap of a finger. It must happen with many small steps in the right direction. I recommend introducing a weekly whiteboard meeting where you systematically work together to eliminate waste in all workflows.
It becomes a sport!